Меры по контролю деформации тонкостенных деталей из алюминиевых сплавов
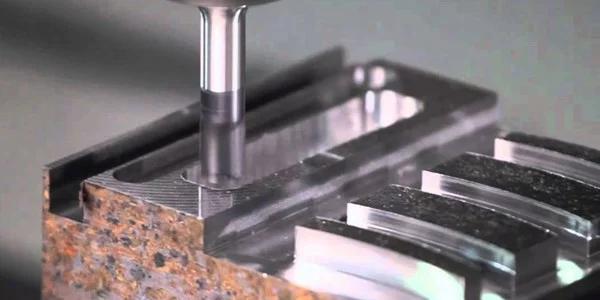
Содержание
Легкость, эстетичный дизайн и высокая механическая прочность — примеры колоссальных преимуществ, которые делают тонкостенные детали из алюминиевых сплавов важным аспектом обрабатывающей промышленности и играют незаменимую роль в индивидуальной обработке алюминия в автомобильной и аэрокосмической промышленности.
Алюминиевые сплавы пользуются популярностью благодаря своей низкой плотности и высокому соотношению прочности к весу, однако недостаточная жесткость тонкостенных конструкций, которые легко деформируются, создает препятствия при изготовлении таких обработанных деталей.
Кроме того, тонкостенные детали имеют низкую температуру плавления во время обработка алюминия на заказ процесс. Высокоскоростное трение, возникающее между материалом из алюминиевого сплава и инструментом, приводит к дополнительному нагреву обрабатываемой детали, что влияет на точность обработки, что является одной из причин, по которой обработка тонкостенных деталей из алюминиевого сплава затруднена.
В статье, основанной на практическом опыте, представлены некоторые меры в списке. Они позволят контролировать деформацию тонкостенных деталей из алюминиевого сплава, чтобы гарантировать эффект пакетной обработки для таких деталей.
1.Контроль температуры обработки
Основными факторами, влияющими на температуру обработки, являются параметры резания: скорость подачи, скорость вращения шпинделя и осевая глубина резания. Эффективно подавить вибрацию можно, регулируя параметры процесса фрезерования. При использовании фрезы подача на зуб в идеале должна составлять от 0,1 до 0,15 мм; кроме того, рекомендуется ограничить глубину резания до 1 мм во время резания — это может помочь достичь лучших результатов обработки с меньшей вибрацией при производстве качественных деталей.
Вибрацию можно эффективно контролировать выбором параметров процесса резания. Не слишком агрессивная скорость вращения шпинделя является ключом к предотвращению вибрации; тщательно выбранная скорость подачи может смягчить внезапные изменения во время обработки и устранить вибрацию за счет увеличения скорости подачи каждой шестерни, что снижает вероятность деформации. Каждый параметр резания оказывает более непосредственное влияние на подавление вибрации, и, следовательно, становится необходимым предварительно оптимизировать все параметры резания.
2. Выбор стандартизированных приспособлений
Выбор приспособлений имеет большое значение при обработке тонкостенных деталей из алюминиевого сплава. Выбор подходящего приспособления может снизить скорость деформации. Несколько важных факторов включают:
Для выбора схемы конструкции приспособления
Проанализируйте опыт обработки тонкостенных деталей из алюминиевого сплава, чтобы установить наилучшие параметры приспособления. Кроме того, при установке приспособления убедитесь, что в точках контакта с деталями из алюминиевого сплава размещены жесткие опорные пластины и эластичные открытые кольца. Это делается для предотвращения повреждений из-за давления на приспособление и снижения вероятности деформации.
При обработке внутренних отверстий в конструкции тонкостенных деталей из алюминиевых сплавов необходимо с внешней стороны конфигурировать усиливающее кольцо, а с внутренней стороны устанавливать эластичное шплинтовое кольцо для достижения эффекта исключения деформации при зажиме.
Контроль за оформлением
Поддерживайте контроль зазора между опорной пластиной и усиливающим кольцом таким образом, чтобы он обычно был менее 0,02 мм; это служит мерой, гарантирующей, что при зажиме упругая деформация тонкостенных деталей из алюминиевого сплава не превысит монтажный зазор (что позволит детали восстановить свою первоначальную форму после обработки). В случае, если деформация все же имеет место, убедитесь, что пластическая деформация находится в пределах допуска.
Равномерное зажимное усилие
При проектировании приспособления для тонкостенных алюминиевых деталей важно учитывать специфические особенности. Например, одной из мер, которую следует рассмотреть, является увеличение средней площади контакта зажимного усилия; это гарантирует, что усилие, создаваемое приспособлением как зажимом, равномерно прикладывается к рабочей поверхности вашей заготовки, тем самым предотвращая деформацию тонкостенных деталей из алюминиевого сплава из-за неравномерной локальной силы. Например, из-за высоких требований к точности и аккуратности при прототипирование медицинских устройствлюбая деформация может привести к серьезным проблемам с производительностью и потенциально поставить под угрозу безопасность пациента.
В частности, фрезерно-расточное приспособление должно иметь специальную функцию. Эта функция делает его контактную поверхность с тонкостенными деталями из алюминиевого сплава очень значимой. В такой ситуации усилие зажима должно контролироваться компрессионным винтом малого диаметра, чтобы предотвратить деформацию тонкостенных деталей из алюминиевого сплава.
Адаптивные приспособления
В процессе обработки из-за трения между инструментом и тонкостенными деталями из алюминиевого сплава повышается температура на контактной поверхности, что приводит к изменению размеров тонкостенных деталей из алюминиевого сплава.
Теперь приспособление может имитировать свою деформацию и при этом иметь возможность свободно растягиваться и сжиматься, что определяет, насколько плотно приспособление может зажимать, что, в свою очередь, также определяет инженерные эффекты при работе с тонкостенными компонентами из алюминиевого сплава.
Учитывая стабильность во время резки, приспособление должно учитывать тепловое расширение компонентов из алюминиевого сплава в радиальном режиме, что может быть достигнуто с помощью системы резиновых колец, разделяющих подвижную позиционирующую пластину и деталь, а также предотвращать любые деформации из-за неэффективности приспособления; используйте осевой режим.
3. Устранение внутреннего напряжения
Тонкостенные алюминиевые компоненты имеют низкую жесткость из-за своей металлической природы. Увеличение жесткости может эффективно избавиться от внутреннего напряжения и предотвратить потерю точности из-за неправильного обращения во время обработки. Производство тонкостенных деталей из алюминиевого сплава является сложным. Независимо от того, как обрабатывается заготовка, внутренние напряжения в конструкции обязательно будут существовать и повышать риск деформации во время обработки.
При обработке сырья с помощью инструмента равновесие внутренних напряжений теряется, и оно становится более склонным к деформации. Однако при его отсутствии внутреннее напряжение выравнивается, поскольку материал не удаляется из заготовки. Такие методы, как использование механической энергии для отжига или старения, используются для обработки тонкостенных алюминиевых деталей. Они действуют как важные процессы, поскольку вызывают изменения напряжений внутри материала, прерывая концентрации напряжений в критических местах, что способствовало бы возникновению или распространению трещин.
Кроме того, некоторые отрасли промышленности используют стратегии предварительной обработки для борьбы с внутренним напряжением. Это процесс, в котором сырье обрабатывается на основе проектных параметров, которые включают допуски на обработку, тем самым уменьшая возможный срез материала при окончательной обработке. Это помогает снизить риск деформации в результате нестабильности из-за несбалансированных внутренних напряжений и, в частности, включает удаление избыточного материала на этапах перед пошаговой обработкой: черновой, получистовой и чистовой обработкой. Таким образом, они способны минимизировать дисбаланс деформации из-за внутреннего напряжения.
Заключение
При обработке этих деталей деформация весьма вероятна из-за высоких проблем, обусловленных собственными свойствами алюминиевых сплавов и сложностью тонкостенных структур деталей. Чтобы исключить такие риски, все используемые приспособления должны быть стандартизированы, поверхность деталей защищена, внутренние напряжения удалены, а последовательности обработки оптимизированы с использованием критериев, основанных на практическом опыте.
Кроме того, непрерывный мониторинг и регулировка силы зажима во время процесса обработки может повысить общую точность и качество производимых компонентов. Использование усовершенствованных датчиков и систем обратной связи позволяет выполнять корректировку в реальном времени, гарантируя, что детали надежно закреплены на месте без приложения чрезмерной силы.